PRODUCT CATEGORIES
CONTACT US
DANBACH ROBOT JIANGXI.INC. Phone:+86-18602162995Tel:+86-0791-88133135
Fax:+86-0791-88221576
E-mail:info@dbhrobot.com
Address:No.811,Chuangxin 3rd road,High-tech district,Nanchang city,Jiangxi province,China
Danba analyzed from five industrial robot control system
DANBACH ROBOT
Controller is the core of the robot system, foreign companies on China's strict blockade. In recent years, with the development of microelectronics technology, the performance of microprocessors is getting higher and higher, and the price is more and more cheap, on the market has appeared 1-2 dollars 32-bit microprocessors.
1, industrial robot control system hardware structure
Controller is the core of the robot system, foreign companies on China's strict blockade. In recent years, with the development of microelectronics technology, the performance of microprocessors is getting higher and higher, and the price is more and more cheap, on the market has appeared 1-2 dollars 32-bit microprocessors. Cost-effective microprocessor for the robot controller has brought new development opportunities, so that the development of low-cost, high-performance robot controller possible. In order to ensure that the system has sufficient computing and storage capacity, the current robot controller to use more computing power of the ARM series, DSP series, POWERPC series, Intel series chips.
In addition, due to the existing general-purpose chip in function and performance can not fully meet some of the robot system in the price, performance, integration and interface requirements, which resulted in the robot system SoC (SystemonChip) technology needs, The integration of a specific processor with the required interface simplifies the design of the system's peripheral circuitry, reduces system size, and reduces cost. Actel, for example, integrates the NEOS or ARM7 processor cores into its FPGA products to form a complete SoC system. In the robot motion controller, its research mainly concentrated in the United States and Japan, and a mature product, such as the United States DELTATAU companies, such as Japan's Peng Li. Its motion controller takes the DSP technology as the core, uses the PC-based open structure.

2, industrial robot control system architecture
In the controller architecture, its research focuses on functional division and functional exchange of information between the norms. In the open architecture of the controller architecture, there are two basic structure, one is based on the hardware hierarchy structure, the type of structure is relatively simple, in Japan, the architecture is divided on the basis of hardware, such as Mitsubishi Heavy Industries Co., Ltd. will Its structure is divided into five-layer structure; the other is based on the functional division of the structure, it will be considered together with the hardware and software, which is the robot controller architecture research and development direction.
3, control software development environment
In the robot software development environment, the general industrial robot companies have their own independent development environment and independent robot programming language, such as Japan Motoman Corporation, Germany KUKA company, the United States Adept company, Sweden's ABB company. Many universities have a lot of research work on the Robot Development Environment, which provides many open source and can be integrated and controlled under the hardware structure of some robots. Many experiments have been carried out in the laboratory environment. Domestic and foreign existing robot system development environment has TeamBots, v.2.0e, ARIA, V.2.4.1, Player / Stage, v.1.6.5.1.6.2, Pyro.v.4.6.0, CARMEN.v.1.1 .1, MissionLab.v.6.0, ADE.V.1.0beta, Miro.v.CVS-March 17.2006, MARIE.V.0.4.0, FlowDesigner.v.0.9.0, RobotFlow.v.0.2.6, etc. Wait. From the perspective of the development of the robot industry, there are two requirements for the robot software development environment. On the one hand, from the end users of robots, they not only use robots, but also want to be able to programmatically give the robot more functionality, this programming is often used in visual programming language, such as Lego MindStormsNXT graphical programming environment and Microsoft RoboticsStudio Provides a visual programming environment.
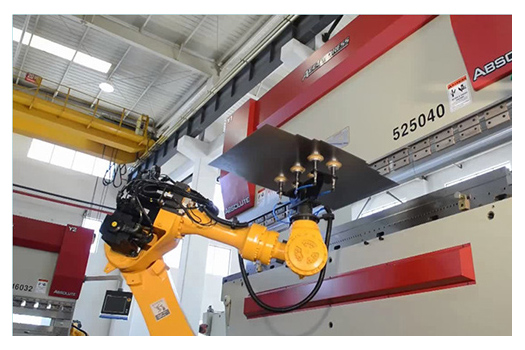
4, the robot-specific operating system
(2) WindowsCE, WindowsCE and Windows series has good compatibility, is undoubtedly a major advantage of WindowsCE promotion. WindowsCE provides a feature-rich operating system platform for building dynamic applications and services for handheld devices and wireless devices. It can run on a wide variety of processor architectures and is generally suitable for applications where memory footprints are limited device of.
(3) embedded Linux, because of its source code is open, people can be modified to meet their own applications. Most of them comply with the GPL, is open source and free. Can be modified slightly applied to the user's own system. There is a huge group of developers, no special talent, as long as understand Unix / Linux and C language can be. The number of supported hardware is huge. Embedded Linux and ordinary Linux is no essential difference, PC hardware used in almost all embedded Linux support. And a variety of hardware driver source code can be obtained for the user to write their own proprietary hardware drivers bring great convenience.
(4) μC / OS-Ⅱ, μC / OS-Ⅱ is a well-known open source real-time kernel is designed for embedded applications can be used for 8-bit, 16-bit and 32-bit microcontrollers or digital signal processor DSP). Its main features are open source, good portability, can be cured, can be cut, preemptive kernel, can be certainty.
(5) DSP / BIOS, DSP / BIOS is a real-time multi-tasking operating system kernel specially designed and developed by TI for its TMS320C6000TM, TMS320C5000TM and TMS320C28xTM series DSP platforms. It is part of TI's CodeComposerStudioTM development tool one. DSP / BIOS mainly consists of three parts: multi-threaded real-time kernel; real-time analysis tools; chip support library. The use of real-time operating system development process, you can quickly and easily develop complex DSP program.
5, robot servo communication bus technology
At present, there is no dedicated servo communication bus in the robot system. In practical application, some commonly used buses such as Ethernet, CAN, 1394, SERCOS, USB, RS-485 and so on are usually used according to system requirements. Robot system. At present most of the communication control bus can be summarized into two categories, namely, RS-485 and line-driven technology based on serial bus technology and real-time industrial Ethernet high-speed serial bus technology.
Previous:Digital Factory, smart and intelligent manufacturing plant
next:none