PRODUCT CATEGORIES
CONTACT US
DANBACH ROBOT JIANGXI.INC. Phone:0086-18801818975Tel:0086-0791-88133135
Fax:0086-0791-88221576
E-mail:info@dbhrobot.com
Address:Nanchang High - tech Zone Innovation No. 811
Analysis of the performance of AGV car
DANBACH ROBOT
The AGV unmanned handling vehicle not only has intelligent safety protection function, but also has the function of transfer and transportation. It is a high-tech unmanned transportation vehicle. The top ten AGV transportation control system consists of a control panel, a directional potentiometer, an operating status indicator, a steering sensor, an evasion sensor, an intelligent electronic control signal sensor, a drive unit, a guide magnetic strip, and a power supply.
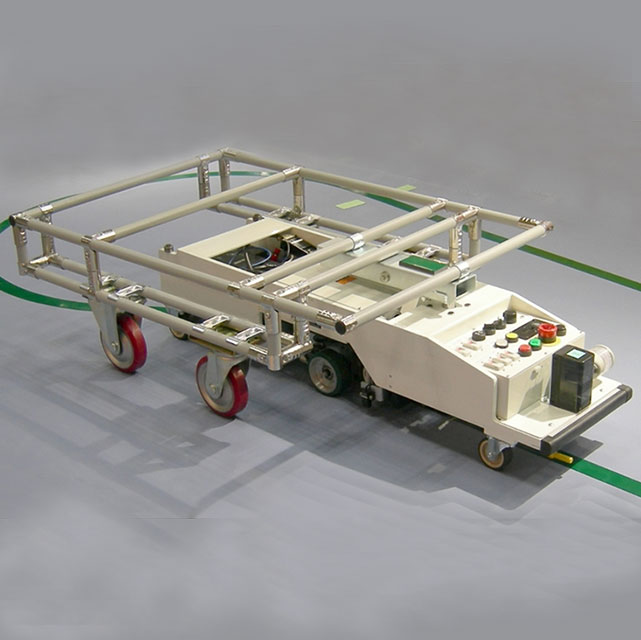
The guidance control of the AGV is the locking of the AGV running track. There are many modes of AGV guidance. For example, using the pointing sensor center point as a reference, tracking the virtual point on the magnetic stripe is one of them. The control goal of the unmanned transport vehicle is to correct the rotational speed of the drive wheel to change the direction of travel of the AGV by detecting the relative position of the reference point and the virtual point, and try to make the reference point above the virtual point. The ability to intelligently lock the tracking and tracking operations, keep abreast of the latest data and status.
After receiving the material handling instruction, the controller system calculates, plans and analyzes according to the stored running map and the current position and driving direction of the AGV trolley, selects the best driving route, and automatically controls the driving and steering of the AGV trolley when the AGV is used. After reaching the loading position and accurately parking the position, the transfer mechanism moves to complete the loading process. Then the AGV car starts and drives to the target unloading point. After the accurate parking, the transfer mechanism acts, completes the unloading process, and reports its position and status to the control system. The AGV car then starts and heads for the standby area. Wait until the new order is received before making the next move.
Previous:Working scene for AGV forklift
next:Forklift AGV application in the supermarket industry